Capsules are the second most frequently used drug delivery dosage form, right after the tablets. Due to their high flexibility in terms of usability and filling material, they are popular in pharmaceutical as well as nutraceutical industry. Even though they’ve been widely used for more than a century, modern shell manufacturing and encapsulation processes still face some challenges for providing perfect capsules, without defects.
HOW A HARD GEL TWO-PIECE CAPSULE IS MADE?
Before we focus on the defects, it is useful to know how a capsule is made in order to understand better the underlying reasons that contribute to a defect on a capsule. In order to get the final product, capsule manufacturing divides into two separated processes of capsule shell manufacturing and capsule filling, which are not necessarily done by the same company.
In most cases, capsule shell manufacturing starts with the preparation of gelatin made from collagen. In the next step, several moulding pins made of standardized steel are dipped into the gelatin for a certain amount of time and certain depth, separately for capsule cap and body. This process is called dipping and lasts just a short period of time before the pins get removed from the gelatin and are transferred towards the drying area while spinning around their axis in order the gelatin gets distributed evenly. In the drying area, pins pass several drying stages so the gelatin achieves desired moisture content. After drying, capsule body and cap halves are stripped off the pins, cut to a correct length and in the final step joined together into a pre-lock position before they get ejected into containers for transport and filling.
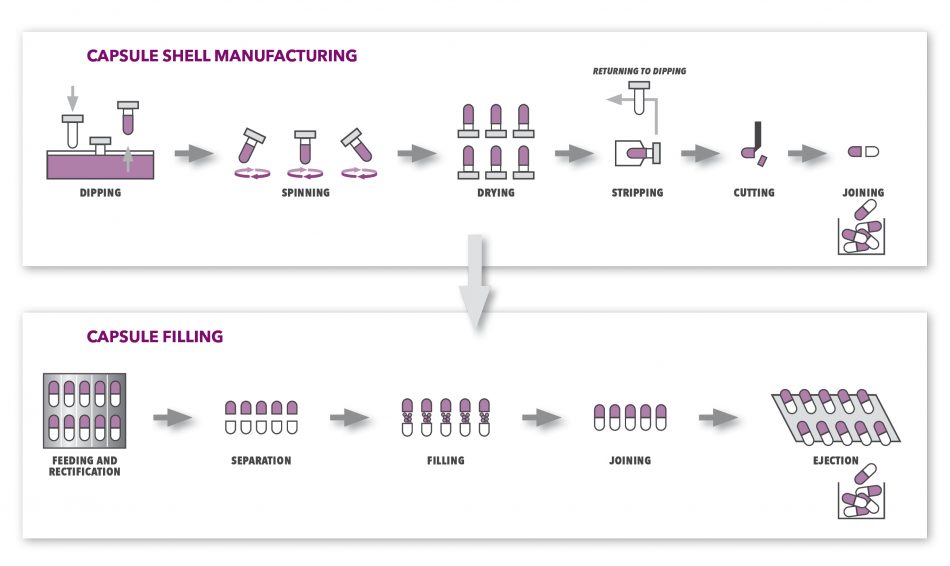
The next process, before capsules can be packed for consumers, is so called capsule filling (or encapsulation) where capsules are actually filled with the desired ingredient which can be powder, beads, granules, pellets, tablets, liquids or a certain combination of these ingredients. This process is done by capsule filling machines and starts with empty capsules being inserted into the machine and aligned so caps and bodies can get separated properly. Further on, capsule bodies get filled with the ingredient and closed with caps. Finally, they are ejected into the container for finished products. When the filling is liquid, prior to packaging, capsules also go through banding process which applies a film of sealing material to the area between the cap and body to ensure the liquid does not leak from the capsule. Voila, the product is ready to be packaged and shipped to its final destination…or is it?
PRESENCE OF DEFECTS
Even though the manufacturing and filling processes have come a long way since the introduction of first capsules in the nineteenth century, both face challenges when it comes to providing defect-free capsules even today. Taking into consideration that modern production machines operate 24/7, producing and filling large quantities of different capsules, it is inevitable, as in all industrial processes, that a certain number of capsules will come out defective one way or another. A capsule can be defective in a number of ways. In our case, we will focus on visual defects on the capsule shell, which are either caused during the capsule shell manufacturing or filling (encapsulation) process. As you can see in the table below, there is a wide range of defects that can be found on hard shell capsules, ranging from major ones that are considered critical and affect performance of the final product, to minor ones that include visual imperfections of the capsule and raise serious doubts about the integrity and quality of the product.
Quality systems used by companies that either produce capsule shells or fill them are usually based on certain statistical schemes or 100% visual inspection, which can be either manual or automated. As we have mentioned already in our article about tablet defects, statistical schemes cannot assure the required quality of each product, that’s why companies rather focus on 100% visual inspection and sorting quality approach. When we speak about inspection of high-volume capsule batches, we hardly imagine doing an accurate 100% visual inspection manually. It is virtually impossible to maintain high quality standards in pharma while knowing the risks of manual inspection. For this reason, companies are nowadays investing more and more into automated capsule visual inspection systems, as for example SENSUM solutions, especially when the product is complex and visually demanding and can be reliably inspected with the help of advanced algorithms.
In the table below, we have prepared an overview of the most common visual hard gel capsule defects we see in our daily work. As you’ll notice, the defects are divided into two groups according to their source, which can be in capsule shell manufacturing or filling process. Furthermore, for each defect we have also determined the reasons for the occurrence.
CAPSULE SHELL PRODUCTION PROCESS
DEFECTS |
PROCESS RELATED CAUSES |
FORMULATION RELATED CAUSES |
Colour deviation |
Improper storage conditions (exposure to light, heat, pH, microbial contamination etc.). |
Relative bad stability of selected dyes and pigments, improper amount of the pigment or improper homogenization of the pigment |
Short body/cap |
Insufficient entry of the body/cap into the collet prior to cutting operation due to wet shell or problem with the collet. |
/ |
Long body/cap |
Caused by a missing knife or a broken knife during cutting operation. |
/ |
Dots/specks
|
Small fragments of shell walls generated during the trimming process getting into the dipping area. This happens during the mold dipping process. Could also be result of a print. |
Foreign materials in the gelatin solution or improper homogenization of the pigment. |
Double cap
|
Loose cap fits over the body of another capsule after one of the caps is loose due to insufficient pre-lock position in joining block. This happens during handling of capsules. |
/ |
Holes/scratch |
Mechanical problems or poor machine setup causing the stripper jaws touching the shell as it moves forward to strip it off during the removal of dried films from the mold pin. |
/
|
Joints/damaged edge/rough cut
|
Caused by a blunt knife during cutting operation. |
/ |
Star ends |
Uneven distribution of gelatin on dip-coated pins or an excessive amount of gelatin solution on the end of the pin. |
Improper viscosity of gelatin formulation. |
Bubbles
|
Improper vacuum or duration of the gelatin bubbles extraction process. |
/ |
Damaged print
|
Improper ink viscosity and applying pressure, uneven flow of the ink, clogged ink jets, incomplete drying of ink etc. |
Improper formulation of the ink blends with a combination of coating ingredients. |
Thin/thick wall
|
Uneven distribution of gelatine on dip-coated pins (thin wall). The pins are dipped twice or are in the gelatin too long (thick wall). |
Improper viscosity of the gelatin solution, insufficient presence of wetting agent. |
Split
|
Caused by uneven drying or an uneven film thickness at the point of split. |
Insufficient amount of plasticizer, low equilibrium moisture. |
ENCAPSULATION/CAPSULE FILLING PROCESS
DEFECTS |
PROCESS RELATED CAUSES |
FORMULATION RELATED CAUSES |
Dents and pinholes (on tips) |
Excessive closing length setting during the encapsulation process, excessive lock length, excessive closing pressure, over-filling of capsules, incorrect pin size or pin configuration, improper storage conditions (moisture). |
Improper mechanical properties of the gelatin, e.g. plastic deformation due to too high water content. |
Crack |
Improper (storage) conditions that favor the transfer of moisture from the capsule shell to encapsulated components, misalignment of the upper and lower capsule segments or incorrect setting of the cap hold-down pin in the joining station. |
Improper mechanical properties of the gelatin due to low amount of plasticizer or low equilibrium moisture or use of hygroscopic components that absorb water from the capsule shell. |
Telescoped |
Unaligned body and cap due to excessive gap in the counter bearing, general misalignment of filling machine components or worn-out machine components, capsule fill weight too high, bad quality of the formed powder slug, high capsule size variation, improper environment conditions (temperature swings) and/or worn-out cap seat or body passage. |
Distorted shape of capsules due to coarse fill components with hard and sharp edges. |
Improperly closed/unclosed |
Improper closing length setting and closing pressure, improper pin configuration. Contamination of the body-cap interface (lock area) and overfilling. |
/ |
Dusty |
Most probably the result of no use of capsule polisher (when filling dusty fill) at the exit chute of the capsule filling machine prior the capsules are discharged into the product containers. |
/ |
Empty |
Malfunction or no presence of safeguards in capsule filling machine which are preventing empty or underfilled capsules reaching exit chute (e.g. load cells, capacitive sensors, strain gage etc.). |
/ |
Damaged band |
Badly tuned banding process, such as improper wheel height and speed, improper processing temperature, improper band thickness, poor/bad band wheel. |
Improper mechanical properties of the gelatin band, e.g. low tensile strength or high shrinkage causing “banana” shaped defects. |
HAVING TROUBLE WITH DEFECTS ON CAPSULES?
See below in videos how our visual inspection systems can help you with that. Go to our PRODUCTS page to find out more about our STREAM and SPINE solution or contact us on [email protected] to speak with our team of experts.
Sources:
– https://www.vitafoodsinsights.com/services/how-troubleshoot-7-most-common-capsule-defects
– https://www.slideshare.net/BhushanGhike/encapsulation-problem-and-remedies-66452012
– https://www.ncbi.nlm.nih.gov/pmc/articles/PMC2750482/pdf/12249_2008_Article_5457.pdf
– https://www.farmacapsulas.com/en/eliminacao-defeitos-mecanicos-no-fecho-da-capsula/
– https://www.pharmapproach.com/manufacture-of-hard-gelatin-capsules/
– https://www.pharmapproach.com/hard-gelatin-capsules-formulation-and-manufacturing-considerations/2/
– https://manufacturingchemist.com/news/article_page/The_colouration_of_tablets_and_capsules/34905
– https://www.slideshare.net/Ramyapriya7/quality-control-of-capsules
– https://www.academia.edu/9833661/Answers_to_10_common_questions_about_capsule_filling
– https://www.researchgate.net/publication/292539476_Capsule_Manufacturing_Technology
– https://falcaoteles.pt/sites/default/files/PDF/HGC%20Technical%20Manual%20version%20Q026-1-2011E.PDF
– https://simplepharmanotes.blogspot.com/2017/10/manufacturing-of-hard-gelatin-capsules.html
– https://basicmedicalkey.com/capsule-shell-manufacture/
– https://www.icapsulepack.com/capsule-filling-machine/
– L. L. Augsburger, S. W. Hoag: Pharmaceutical Dosage Forms: Capsules, CRC Press, 2017
– https://tabletscapsules.com/wp-content/uploads/pdf/tc_20190101_0012.pdf
– http://proddownloads.vertmarkets.com.s3.amazonaws.com/download/88b9d920/88b9d920-52d8-4e7a-aa83-a149003c0f61/original/aaps_t3427_haibowang.pdf
– http://jddtonline.info/index.php/jddt/article/view/2794/2276
– https://www.speronline.com/japer/Articlefile/224.pdf