The concept of Industry 4.0 is not new to the modern manufacturing environment and literature. It has been around since its introduction by the German government in 2006 as its high-tech strategy vision of the country and economy as a whole. It was a roadmap for the German manufacturing industry to become more globally competitive and a way to digitally transform their society. As the years passed by, the concept started to gain interest also in other parts of the world, especially with the introduction of high-tech innovations that are now one of the backbones and accelerators of the Industry 4.0 concept, i.e. IoT, cloud computing, big data and AI. It is such an important change in the industrial world that Industry 4.0 is also commonly considered as the fourth industrial revolution.
INDUSTRY 4.0 IN A NUTSHELL
Industry 4.0, or also known in the industrial world as Smart Factory, is an information intensive transformation of manufacturing, putting data at the core of the concept. It is an interconnection of the physical world (machines, materials, people etc.) with the digital world (computers, data, IT systems etc.) via cyber-physical (production) systems, or CP(P)S in short. The latter enable real-time data collection, analysis and control not only of the production environment, but of the entire supply chain from raw materials to the end consumer with the help of IoT tools. It is a computer system that integrates a physical object into the corresponding cloud-based algorithms. In this way, each device has its own digital twin that reflects the device in the physical world and can simulate the status of the whole system, thus enabling real-time optimization and prediction for autonomous decisions and accelerate product design and manufacturing. In other words, with the help of digital twins, companies can quickly and at low cost simulate any part of a production process, machine or product in a virtual world and optimize it before they actually built it.
Furthermore, in the Industry 4.0 concept, the entire supply chain is interconnected horizontally (from the first supplier to the end consumer) and vertically (from the field level to the enterprise planning level). With this interconnectivity, the entire supply chain and production environment should achieve a certain level of autonomy and, with the help of AI, be able to learn from all the data collected, control itself and provide necessary and timely information to every stakeholder in the production process (or supply chain) in order to achieve the best possible productivity, efficiency, flexibility, quality and speed, while at the same time considering the feedback from the customer. Systems are therefore able to predict potential problems before they arise – moving from preventive to predictive maintenance, track and optimize assets as they move through the supply chain, simulate processes with real-time data, machines are communicating and moving autonomously etc. The possibilities and benefits of the Industry 4.0 concept are truly enormous and, in some cases, for the current state of technology and legislation around the world, borderline futuristic. It is also a general understanding that the Industry 4.0 does not only focus on the above mentioned production-based parameters, but its concept should reach beyond that, leading to entirely new business models, which are supposed to be one of the main outcomes of the fourth industrial revolution. One of such models is mass customization, where companies are being able to produce (partially) customized products for their customers, but with the help of Industry 4.0 technologies, keeping a low unit costs of mass production.
FOUR LEVELS OF TECHNOLOGY INTEGRATION
As mentioned in the beginning, Industry 4.0 is not a concept that exists by itself or a standalone technology, but rather a system backed by a number of technologies that together accelerate, support and enable the Smart Factory idea. We could think of it as the ultimate level of technology integration in an industrial environment. To understand this better, we can look at the Industry 4.0 concept as four levels of technology integration, with Smart Objects being the first and most basic level.
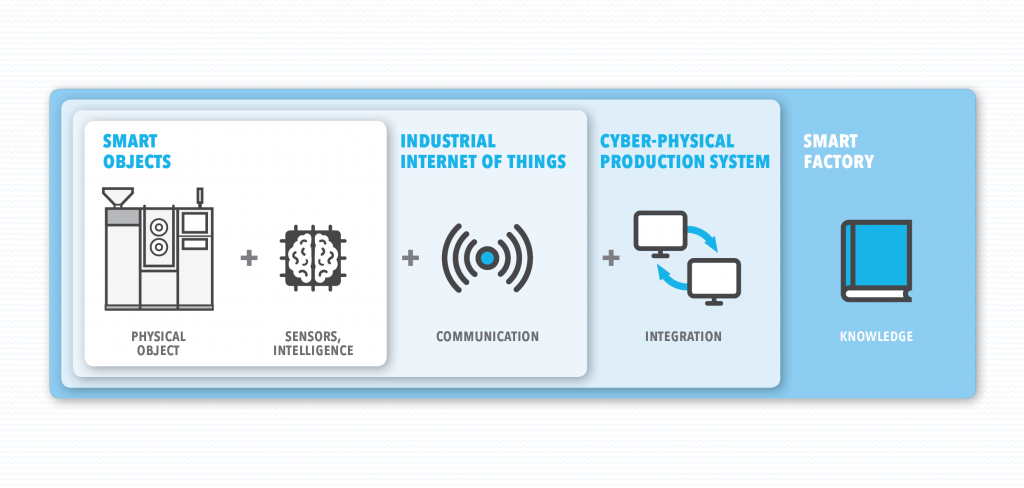
Smart objects are field devices, machines, equipment and products equipped with their own local intelligence in a form of microprocessors, software, PLCs, sensors, etc. that enable them to collect data of themselves and their environment. Connecting these smart objects using wireless sensor networks over the internet gave birth to the (Industrial) Internet of Things (IIoT), creating a network of physical objects that can connect and cooperate with each other. Supported by a software solution, the IoT network already provides the ability to control and analyse the production environment. In a modern pharmaceutical production floor, we could imagine the IIoT as a network of production machines, where each of them is capable to communicate with the rest of the production environment, sending and receiving data from the central production system or other machines that are part of the same production process.
With the introduction of technologies such as Cloud Computing, AI, Big Data Analytics etc., the capabilities of the IoT concept reached a whole new level. New technologies enabled much greater integration of physical and software components and gave birth to Cyber-Physical Systems (CPS) and its Digital Twin. CPS is IoT on steroids, since, in general, we again speak about the network of smart objects (things) which collect their own information and information from the environment, but this time the information is sent to a special computer system that creates real-time cyber replicas of the physical system. This system has enormous computational capabilities and computes all the data received, notifies the physical systems about the findings, reconfigures the system parameters, sends control commands etc., all this independently and autonomously. Nevertheless, all this computational power and autonomous environment has no use if we are not able to enhance the industrial performance and, most importantly, decision making based on the information collected by the whole system. It is the knowledge and information collected from all supporting levels that create the Smart Factory, leading to new business models, insights about the supply chain and production environment. One of such examples is 1.400% productivity increase in one of the Siemens Smart Factories in Amberg, Germany.
The Industry 4.0 is an information driven transformation of the industrial environment that brings numerous opportunities into the industrial world. With its interconnection of the physical and digital worlds, supported by the latest state of the art technological advancements, companies now have the opportunity to take their business (models) to the next level.
Sources:
– Industry 4.0: the fourth industrial revolution – guide to Industrie 4.0. Accessed on https://www.i-scoop.eu/industry-4-0/
– What is Industry 4.0—the Industrial Internet of Things (IIoT)? Accessed on https://www.epicor.com/en/resource-center/articles/what-is-industry-4-0/
– Networks for Cyber-Physical Systems and Industry 4.0. Accessed on: https://www.comsoc.org/publications/magazines/ieee-communications-magazine/cfp/networks-cyber-physical-systems-and
– Hemanth Kumar, S. et al (2020). Adaptations of Pharma 4.0 from Industry 4.0. Drug Invention Today. Accessed on http://jprsolutions.info/files/final-file-5e91ed7d502397.52346272.pdf
– Barenji, R. V., Akdag, Y., Yet, B., & Oner, L. (2019). Cyber-Physical-based PAT (CPbPAT) framework for Pharma 4.0. International Journal of Pharmaceutics. Accessed on https://sci-hub.do/10.1016/j.ijpharm.2019.06.036
– https://us.acrofan.com/detail.php?number=259821
– Padovano, A., Longo, A., Nicoletti, L., Mirabelli, G. (2018). A Digital Twin based Service Oriented Application for a 4.0 Knowledge Navigation in the Smart Factory. International Federation of Automatic Control. Accessed on https://www.sciencedirect.com/science/article/pii/S2405896318315143
– https://www.forbes.com/sites/insights-teradata/2019/07/08/revolution-on-the-siemens-factory-floor/?sh=150f62df5648
– Revolution on the factory floor. Accessed on https://www.researchgate.net/publication/312069858_Industrie_40_and_Smart_Manufacturing_-_A_Review_of_Research_Issues_and_Application_Examples
– K. M. Alam and A. El Saddik (2017). C2PS: A Digital Twin Architecture Reference Model for the Cloud-Based Cyber-Physical Systems. IEEE Access. Accessed on https://ieeexplore.ieee.org/document/7829368
– S. Iarovyi et al (2016). Cyber–Physical Systems for Open-Knowledge-Driven Manufacturing Execution Systems. Accessed on https://ieeexplore.ieee.org/document/7430247